Two Mondays ago, on January 4, the Department of Trade and Industry (DTI) announced provisional safeguard duties in the form of a cash bond amounting to P70,000 that would be imposed on every imported passenger car, and P110,000 on every imported light commercial vehicle (LCV) for a period of 200 days from the issuance of an order from the Bureau of Customs.
DTI chose to impose safeguard duties after it evaluated a petition filed by the Philippine Metalworkers’ Alliance. Under Republic Act 8800 or the Safeguard Measures Act, the government can impose safeguard measures to protect local industries from threat of serious harm from increased imports of similar products.
What can happen once the additional duties under the Safeguard Measures Act are imposed?
On the short term, car prices will go up—as they always do when new taxes or duties are introduced, as we saw just four years ago when the TRAIN Law came into effect. Higher prices result in lower demand. And we saw just what lower demand can do to existing businesses in this pandemic—business closures and personnel layoffs.
On the long term, it is hoped—and this is a big hope—that car companies will turn back to local manufacturing to avoid the import tariff and continue selling at current prices.
Why will additional import duties not work?
This is only my opinion (as someone who has both worked for and covered the industry since 1990). But first, a backgrounder: In the early 90s, the Philippines and Thailand competed over Ford and General Motors—America’s two largest carmakers who wanted to set up shop in Southeast Asia. Ford chose the Philippines (and put up its Sta. Rosa plant) while GM put up its huge Rayong plant in Thailand—which would eventually be called the Detroit of Asia.
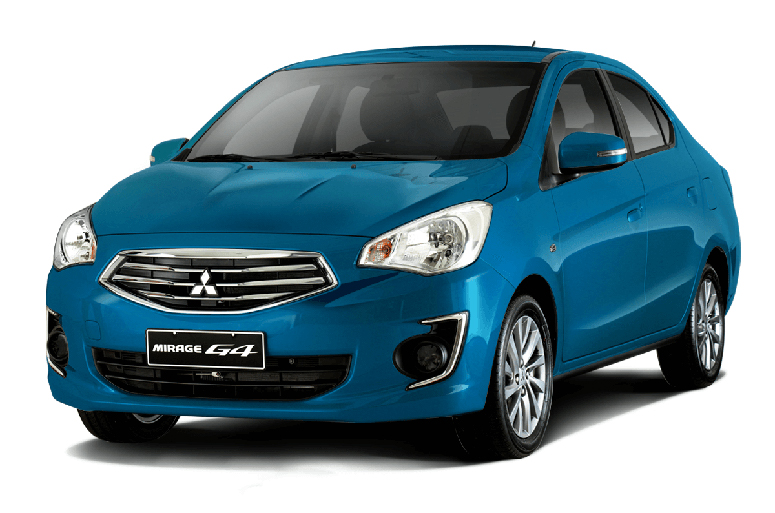
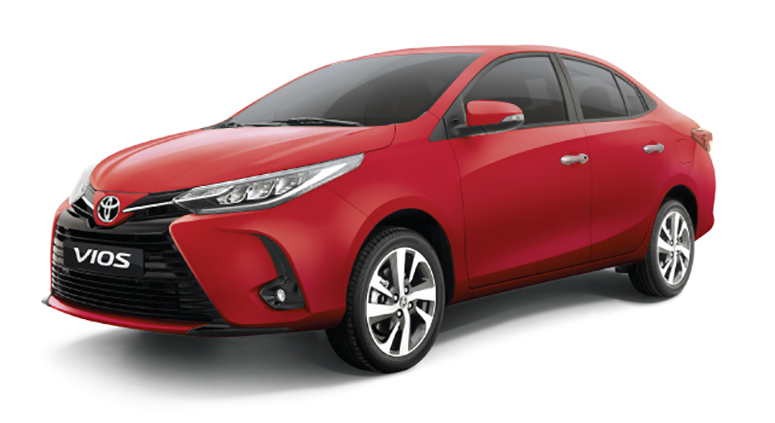
Twelve years after Ford started operations in Sta. Rosa (and after exporting 80,000 vehicles to Thailand, Malaysia, and Indonesia worth over US$1 billion), they shut it down. That Sta. Rosa plant is now owned by Mitsubishi for the production of the Mirage. GM, meanwhile, announced last year its ceasing of operations in Thailand. Why? Economies of scale has been lost. Yes, even for mighty GM in a Thai market that’s three times bigger than the Philippines’.
In the 90s also, we had a Colgate plant near where Rockwell is now. That plant has long been closed and most Colgate-Palmolive products now come from Thailand. Ditto Procter & Gamble products. If government slaps safeguard taxes on toothpaste and shampoo, will those multinational companies start making them here again? I seriously doubt it.
What the consumers will get are just higher priced products. And that is exactly what will happen when imported vehicles are taxed as a safeguard measure.
The writing was on the wall 10 or even 20 years ago. These are the global companies that once had manufacturing plants in the Philippines in the 90s and early 2000s (and even recently): BMW, Kia, Mazda, Daihatsu, Goodyear, Ford, Nissan, Honda. Those factories and assembly plants are all gone now.
To think that the temporary imposition of tariffs would result in a turnaround of operations to bring back local assembly and manufacturing is incredibly overreaching. It’s actually idealistic bordering on the deluded.
Ironically, it will not even help the ailing parts makers, the very industry this safeguard tariff is supposed to help. (Unless the government doles out their additional revenues from the safeguard tariff directly to the parts makers. Good luck with that.) No, what the safeguard tariff actually is, is a penalty on both the car companies and the consumers who buy their products. But will it result in the return of local manufacturing, whether in the near or long term? No.
Why has the Philippines lagged behind?
Obviously, economies of scale. A mid-range Thai-made pickup (all locally available pickups—except the Ford F-150—are made in Thailand now) currently sells for approximately P1.2 million. If the Philippines were to make a local Hilux, Ranger, or Navara, that same truck would probably cost around P1.5 million—again because we make far fewer units of them compared to Thailand. Simple economics.
Other major reasons why manufacturers are closing down their Philippine plants are:
Ease of doing business—The Philippines has some of the most red tape- and graft-ridden government agencies and procedures.
Challenging logistics—Traffic and other logistics-limiting factors literally paralyze every aspect of a business operation.
Unstable and unpredictable government regulations—One moment they’re giving tax breaks; the next moment they’re slapping additional taxes and duties—making it hard for corporations to make long-term business plans.
These, and more, are what need to be addressed should we want the car industry—or any other industry for that matter—to restart local manufacturing. Not protectionist safeguard tariffs.
In any case, it takes anywhere from five to 10 years for a company to decide to establish a manufacturing facility and for the first vehicle to roll off said plant. So a new local plant won’t happen anytime soon.
How can we help the parts-making industry?
This is where I promised a possible win-win solution. The local parts makers have seen a drastic drop in their outputs from the mid 90s, when only 20 percent of car sales were comprised of imported cars. Today, 88 percent of the total cars sold in the Philippines are imported.
Not surprisingly, the number of members in the Philippine Auto Parts Maker Association has dropped from 128 in 2015 to just 49 in 2020—some of which are in a “No Commercial Operations” status due to the absence of demand. Companies have folded and employees have lost their jobs.
Buy why do the parts makers have to rely solely on new car manufacturing (especially when it’s painfully obvious that it’s not economically and fiscally feasible) to keep themselves viable? A new car model can realistically be produced in the thousands (or in the rare case of models like the Vios and Mirage, in the tens of thousands). But there are over 12 million cars registered under LTO. Factor in the unregistered cars and you’re looking at a massive 20 million potential customers. And the parts makers don’t necessarily have to transform into retail businesses as they can still continue to work with the manufacturers to become accredited OE after-sales manufacturers.
What would it take?
The car companies will have to work just as closely with the parts makers to enable the latter to produce world-class OE-quality components and spare parts. The challenge is two-fold:
From the end of the car companies, they will have to allow the localization of their spare parts by Philippine-based Filipino-owned companies. This may be counter-productive to their own internal quotas—set by their mother or regional headquarters—for original brand-name—and usually imported—spare parts sales (which is a major revenue generator for them). But if the car companies truly want to support local industries in their country of operations, they must be willing to do this—and even sell the locally produced parts under their own brand.
For the parts makers, they must meet global standards. I remember when the Philippines was a major producer and exporter of world-class wiring harnesses with Yazaki-Torres. UE Toyo used to make world-class radiators and coil springs. Locally made Goodyear tires performed as well as their imported counterparts. Filipinos can and will produce globally competitive products. But we need support from the car companies. It is precisely this mutually rewarding global company-local supplier business model that made China the automotive powerhouse it is now. Technology transfer is essential.
What can be produced locally?
A typical car is made up of more than 30,000 parts. Multiply that with over the 12 million cars registered locally and you’ve got all the economies of scale you can get—a staggering 360 billion possible parts to make. Car companies can even corner spare parts sales for their latest models and just allow local production of parts for its out-of-market/phased-out models.
That’s still a lot of parts: sheet metal for hoods, trunk lids, tailgates, and doors; glass for windshields and windows; rubber parts for tires, insulations, and weatherstripping; plastic parts for bumpers; electrical parts like wiring harnesses, headlamps and taillamp assemblies, power window switches, wiper motors, alternators, and batteries (Motolite is absolutely booming now); engine and chassis sensors (almost all the Check Engine warning lights are due to faulty sensors); brake parts like discs, drums, pads, and linings; suspension parts like coil and leaf springs, tierod ends and ball joints, bushings, and struts and shock absorbers; transmission parts like clutch discs, pressure plates and release bearings; engine parts like pistons, pistons rings, valves and gaskets; interior parts like seats, carpeting, and upholstery; aircon components like compressors, evaporators, condensers, and cooling coils; and of course, paint.
I honestly don’t understand how parts makers claim they have nothing to make.
Ultimately, it needs cooperation from two industries and the government to help solve the problem of our struggling parts making industry. But a solution is always there. It just needs open minds.
End result? No more “no economies of scale” reasons or excuses why it can’t be done. Just more factories. More plants. More jobs. More business. For everyone.